What to Expect From the Floor Coating Process
Transform Your Floors
The floor coating process is a transformative solution that can take even the most worn-out concrete surfaces and make them look brand new. At Rock Solid Surfacing, our comprehensive process leverages advanced polyurea and polyaspartic coatings to offer long-lasting protection, aesthetic appeal, and easy maintenance. Here’s what you can expect from this multi-step, high-performance process.
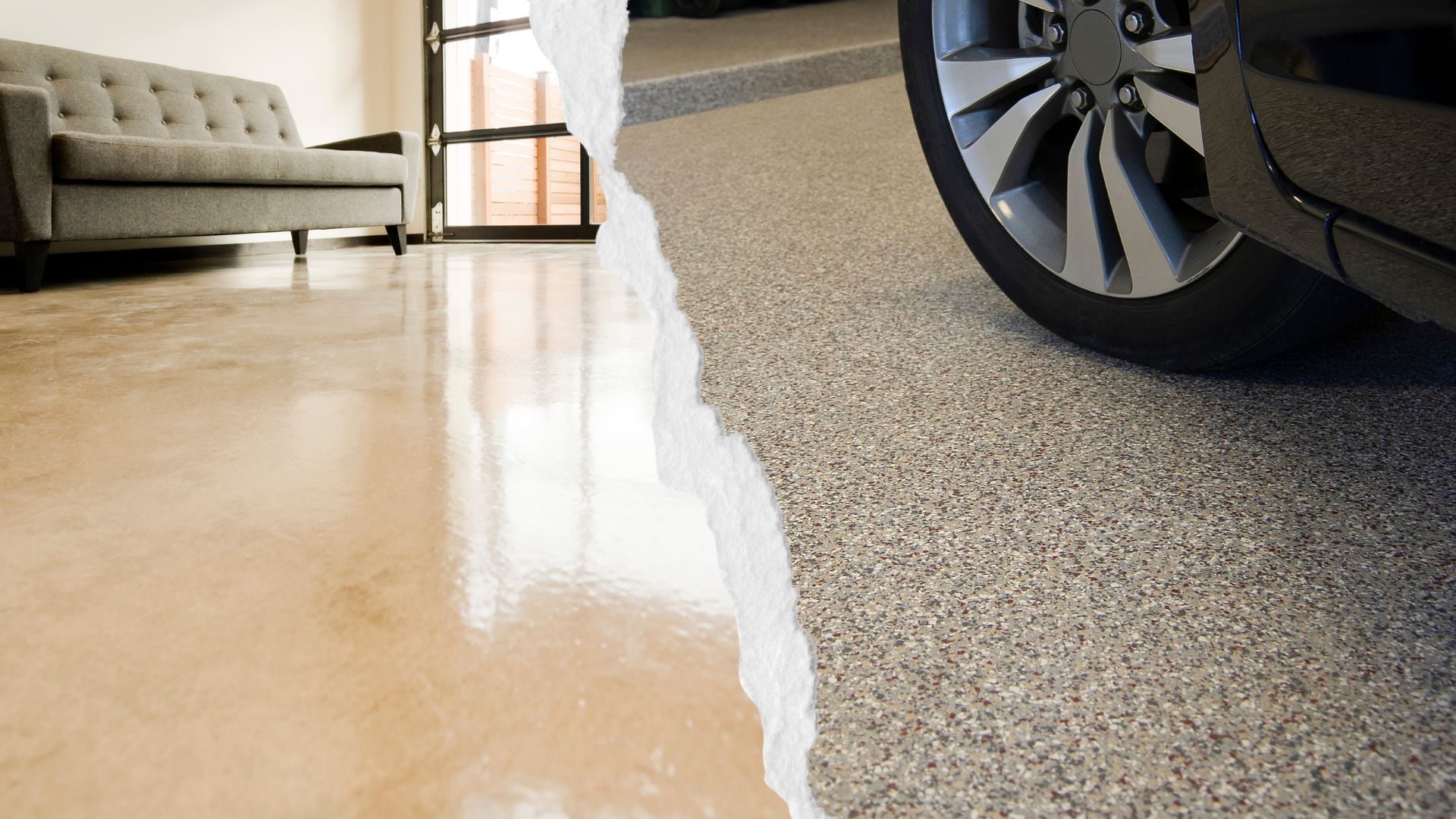
Step 1: Floor Restoration
Whether it’s a new floor or one that’s been subjected to years of wear, our restoration approach ensures a solid foundation for coating. Concrete floors, despite being hard, are porous and vulnerable to decay from road salts, moisture pressure, and freeze-thaw cycles. These conditions can lead to cracks and gradual degradation. Our process starts by cleaning and filling all cracks with a proprietary polyurea filler that absorbs into the crack walls and cures below grade, forming a deep, moisture-resistant barrier. This blocks moisture pressure, which is crucial for preventing delamination and maintaining the longevity of the final coating.
Step 2: Surface Preparation
Proper surface preparation is essential for a flawless finish. We use professional grinding equipment paired with a dustless vacuum system to grind the concrete to a smooth, flat surface. By removing high and low spots, we create a level floor that avoids water pooling and ensures a flawless look. This dust-free method is not only environmentally responsible, but also essential for preparing the floor to securely bond with the polyurea/polyaspartic coating.
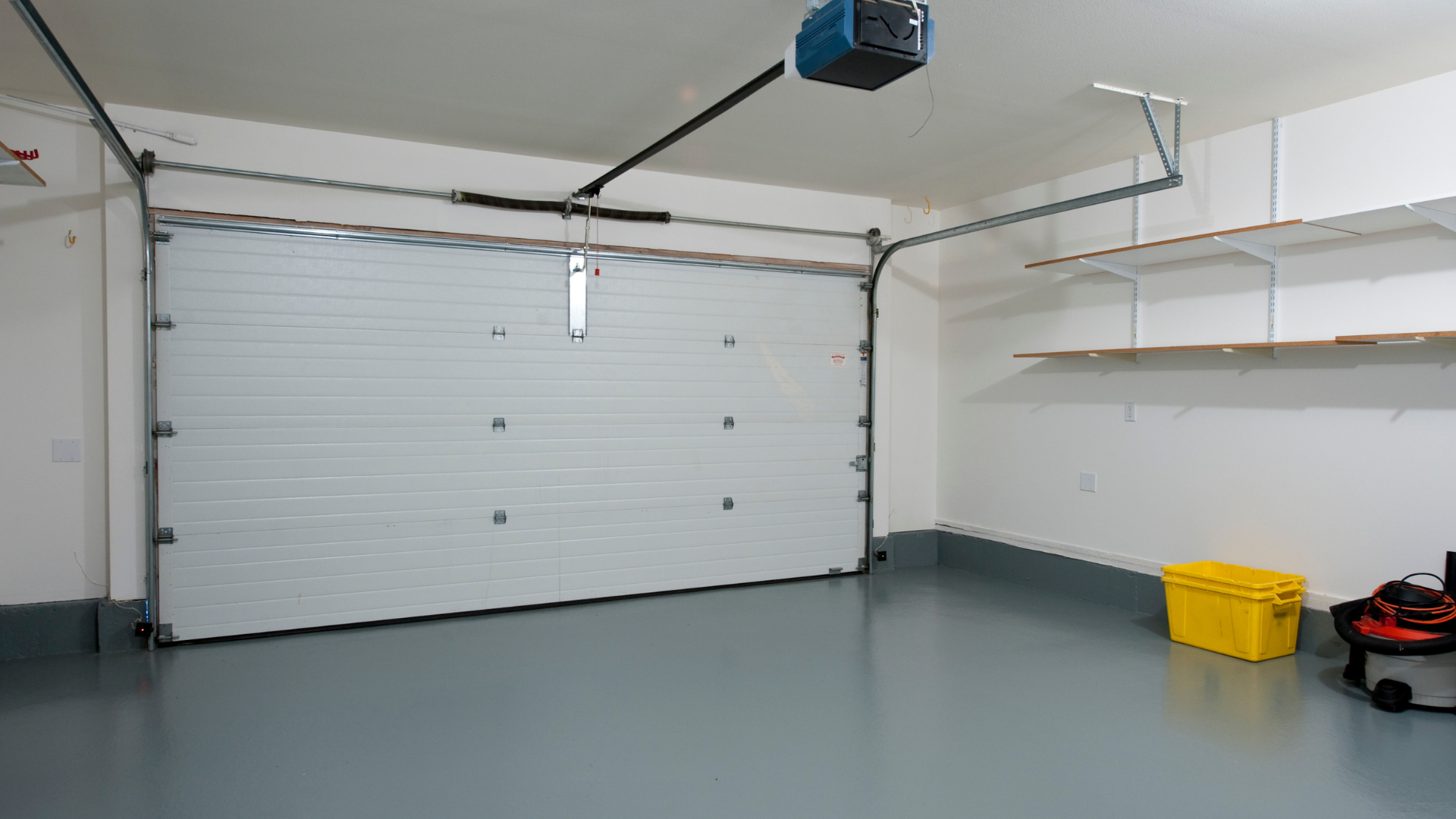
Step 3: Edge Molding
To further enhance the durability and cleanliness of your space, we offer edge molding. The edges of the floor are treated and coated, creating a “pan” effect that prevents water from seeping under walls or damaging drywall. This is especially beneficial for spaces prone to spills or where frequent washing is needed. This step reinforces the waterproof integrity of the floor and makes for easy cleaning.
Step 4: Decorative Coatings
After preparing the surface, we apply a primer coat that absorbs into the concrete, sealing off moisture pressure points that could otherwise weaken the floor’s integrity. We then add decorative chips to achieve a desired look, with options ranging from simple one-color schemes to intricate designs like terrazzo or quartz effects. The final clear coats lock in these decorative elements, creating a beautiful, resilient surface that complements the aesthetics of any space.
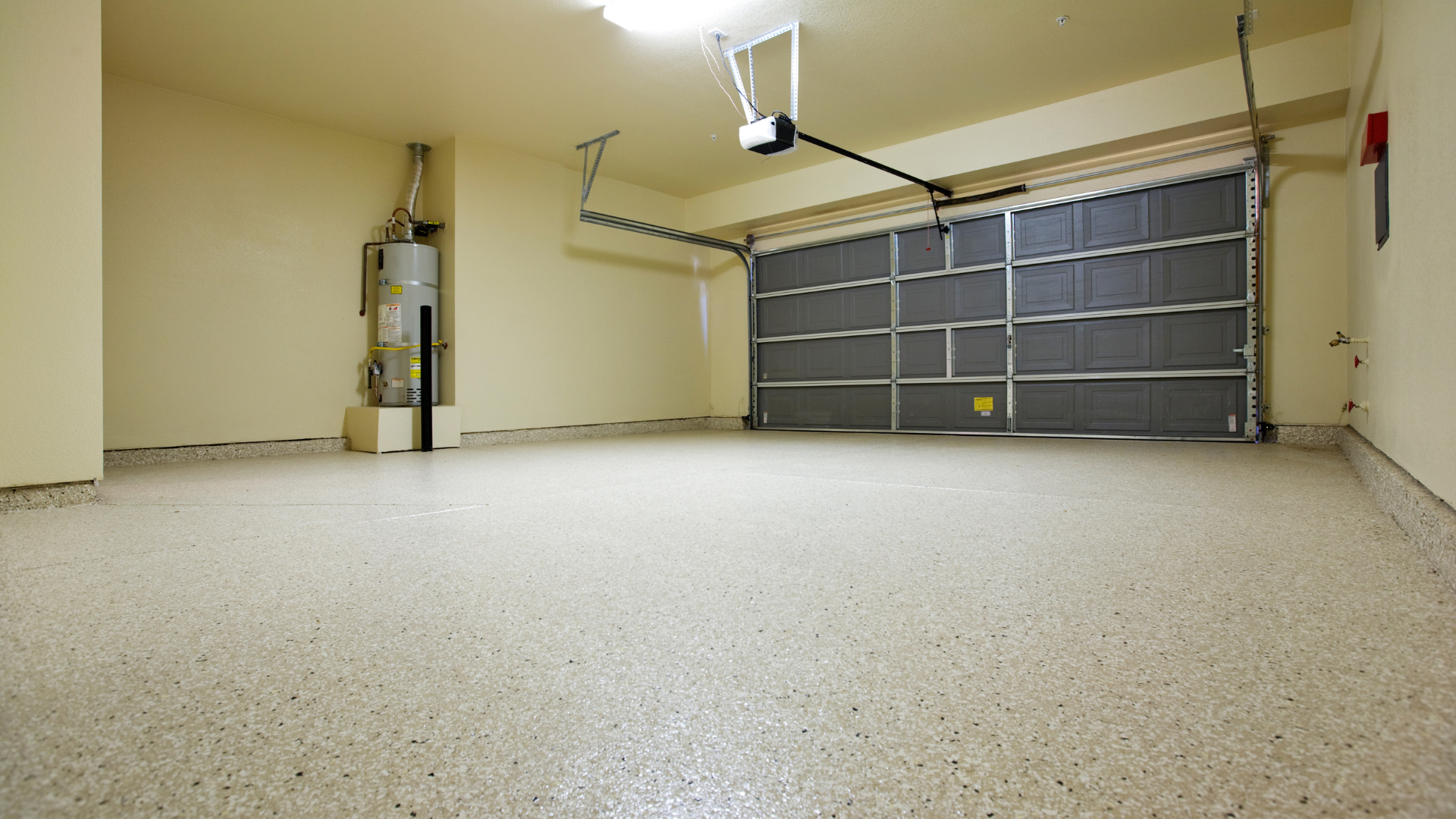
Step 5: Non-Slip Coating
Safety is a top priority, especially for high-traffic areas. Our coatings include a non-slip aggregate embedded in each layer, ensuring that the floor meets or exceeds OSHA standards for slip resistance. This added traction reduces the likelihood of accidents, providing peace of mind for both residential and commercial spaces where slip-and-fall risks need to be minimized.
Step 6: Easy Cleaning and Maintenance
Once installed, your new floor coating will be remarkably easy to maintain. Simple cleaning with water, a small amount of liquid soap, a squeegee, and a broom will keep the surface looking fresh and vibrant for years. The polyaspartic/polyurea surface resists frayed micro-scratches, which can trap dirt and bacteria, making cleaning much more effective. Unlike traditional epoxy coatings that can darken and lose reflectivity over time, our coatings maintain their clarity, light reflectivity, and cleanliness.
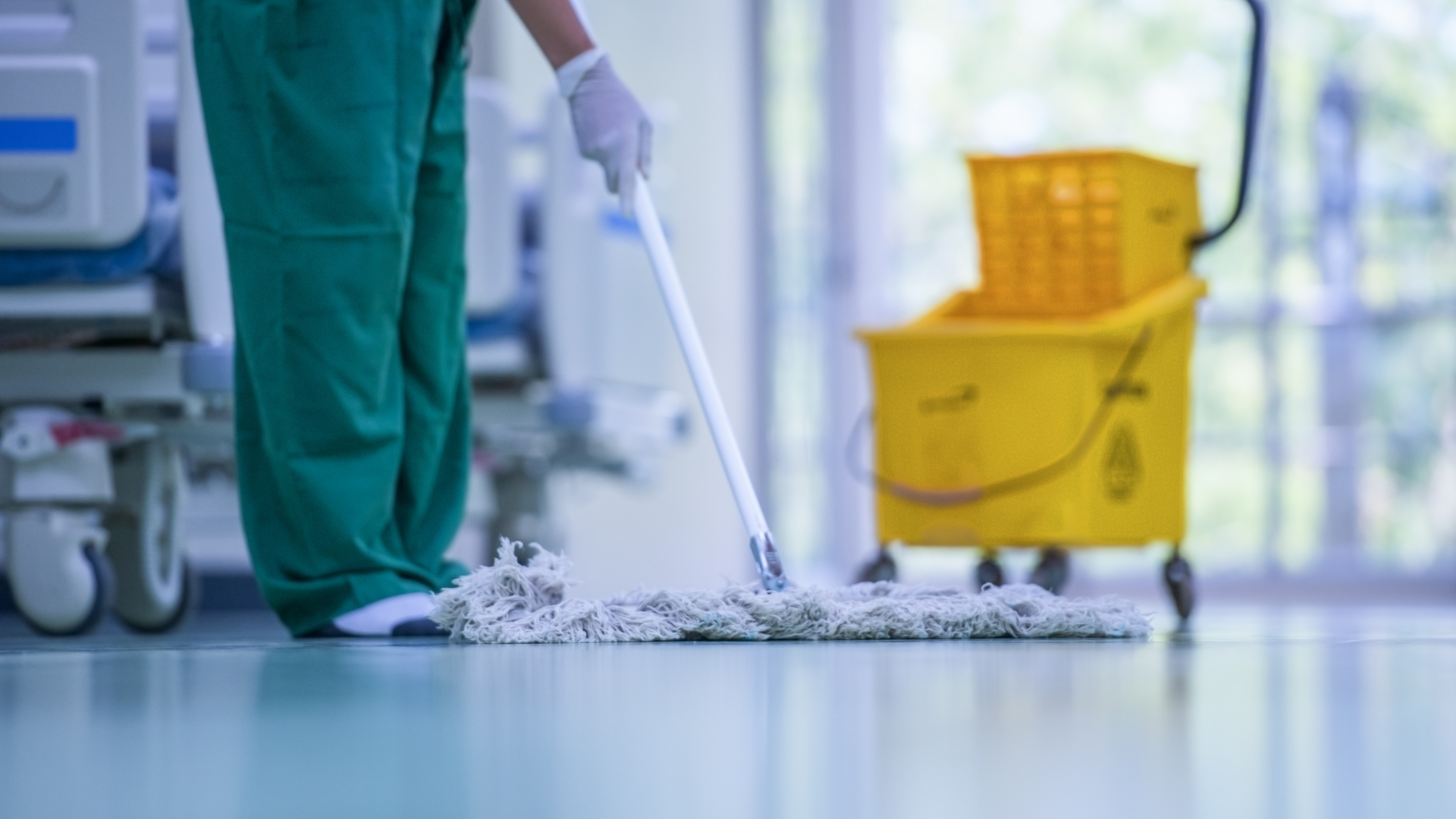
Polyaspartics and Polyurea: The Core of Our Coating System
Our advanced coatings utilize both polyurea and polyaspartic components to deliver a superior floor coating. Here are some unique benefits of this combination:
- Low Bacteria Growth: Thanks to tight cross-linking in the chemical structure, micro-scratches remain straight and don’t trap dirt or bacteria. This results in healthier floors, especially important in environments like hospitals, kennels, or any area where sanitation is crucial.
- Exceptional Adhesion: Polyaspartic/polyurea coatings “wet” into the concrete, creating a seal that resists moisture vapor pressure. This capillary action directs moisture horizontally under the concrete rather than vertically, preventing damage and reducing indoor humidity for better air quality.
- Chemical Resistance: The high solids content and durable cross-linking in our coatings make them resistant to chemicals, road salts, and other harsh substances. This makes our coatings ideal for cold climates or areas with heavy foot and vehicle traffic, as they withstand even the most challenging conditions.
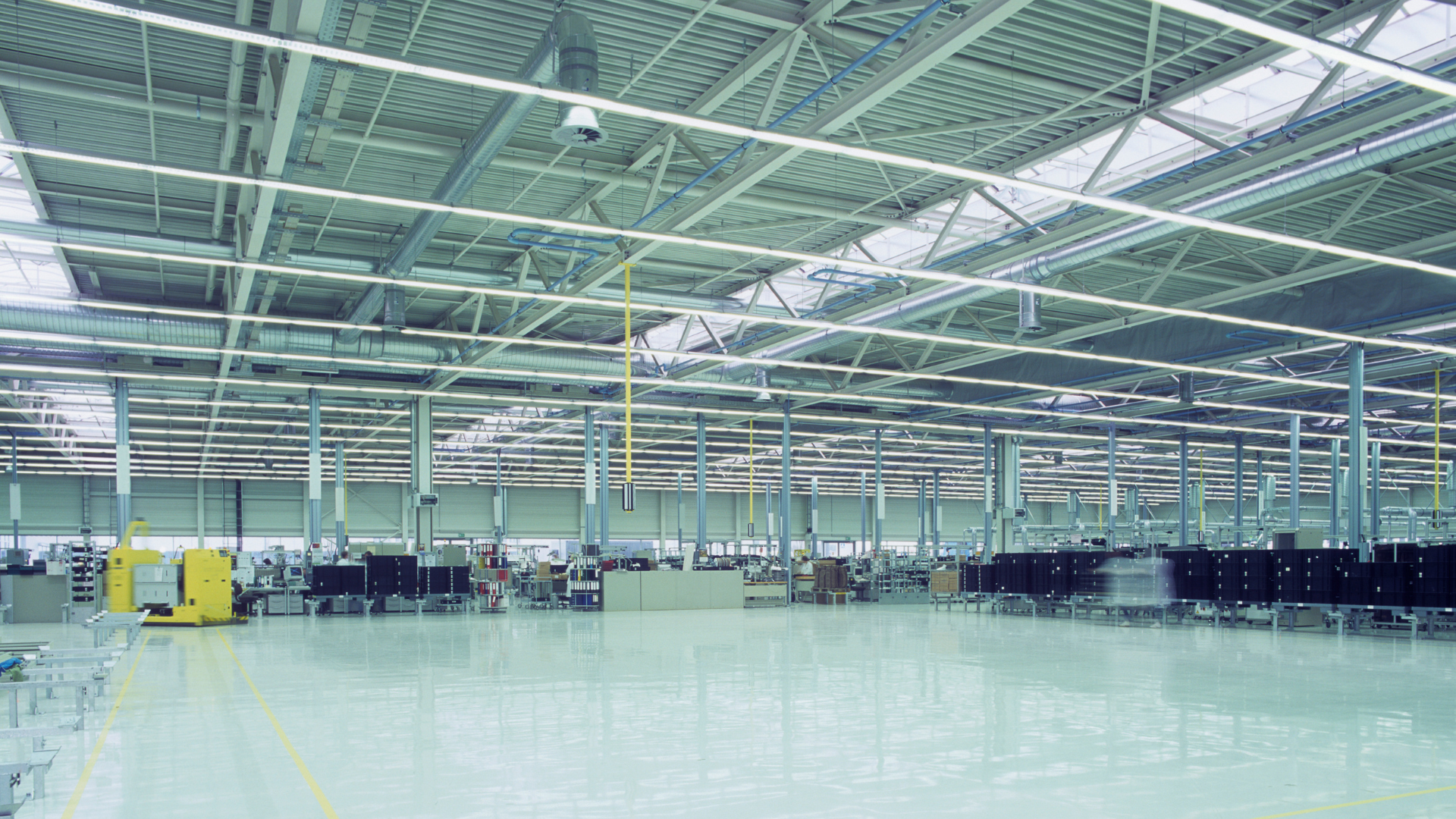
- Zero VOCs: Our coatings contain no Volatile Organic Compounds (VOCs), making them safe for both indoor and outdoor use without releasing harmful emissions. This eco-friendly feature is especially beneficial for residential and commercial spaces concerned about air quality.
- Rapid Cure: Unlike traditional epoxy that may take several days to cure, our polyurea/polyaspartic coatings can be applied and ready for use within 24 hours. This allows for minimal downtime, enabling business owners and homeowners to resume activities without prolonged disruption.
- Customizable Aesthetics: Beyond just durability, our coatings offer incredible versatility in style. Choose from a range of decorative chips, colors, and designs to customize the look of your space. For businesses, custom graphic inlays or logos can be added to create a branded, professional appearance.
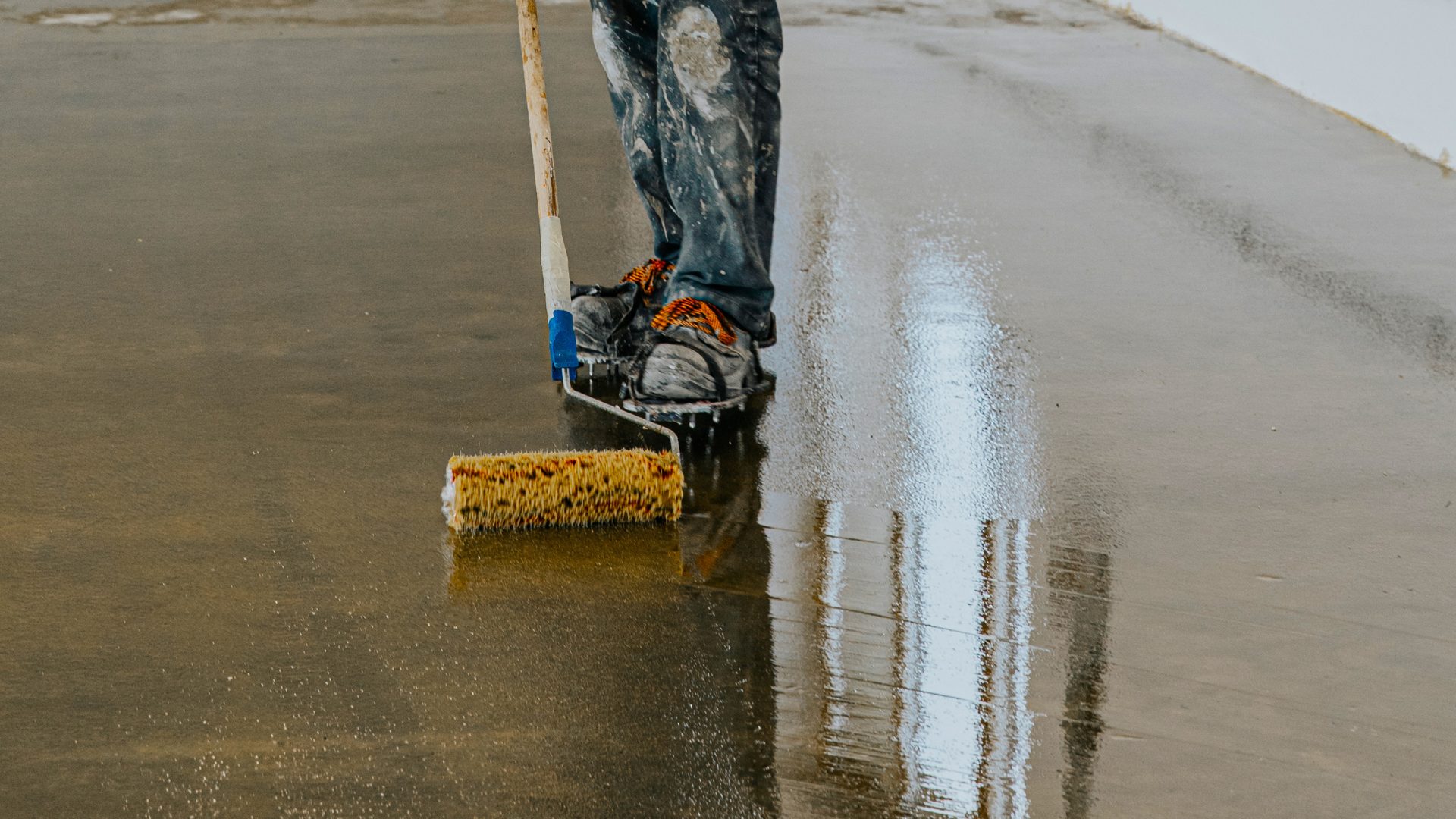
Investing in a Quality Coating Process
Our floor coating process not only transforms the look of your floor but also adds substantial value to your property. With a strong, durable, and easy-to-clean surface, your space becomes more functional, safer, and visually appealing. The benefits extend beyond aesthetics—this process enhances durability, reduces maintenance, and promotes a healthy indoor environment.
With Rock Solid Surfacing, you’re investing in a flooring solution that’s built to last, customized to your needs, and supported by industry-leading technology.
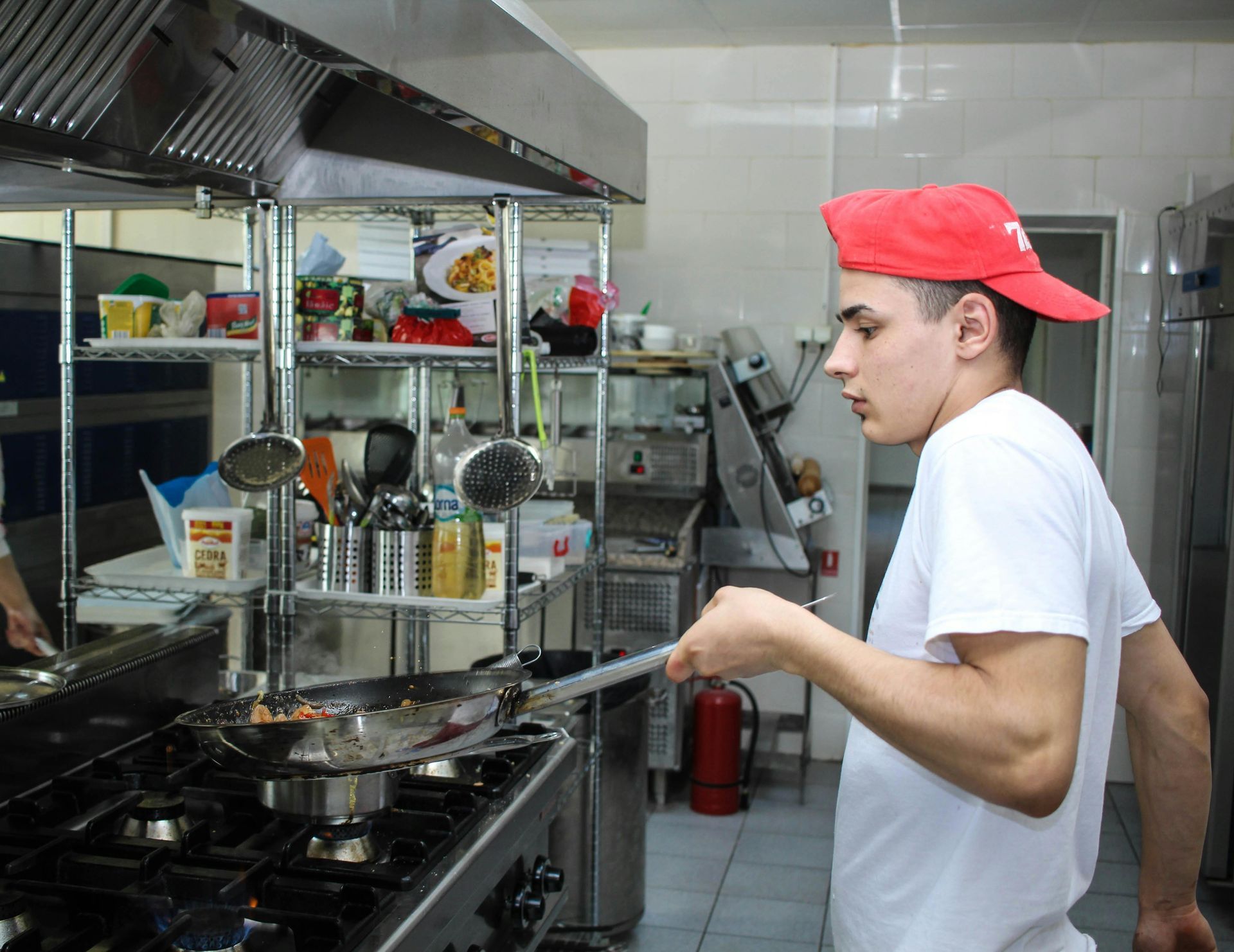
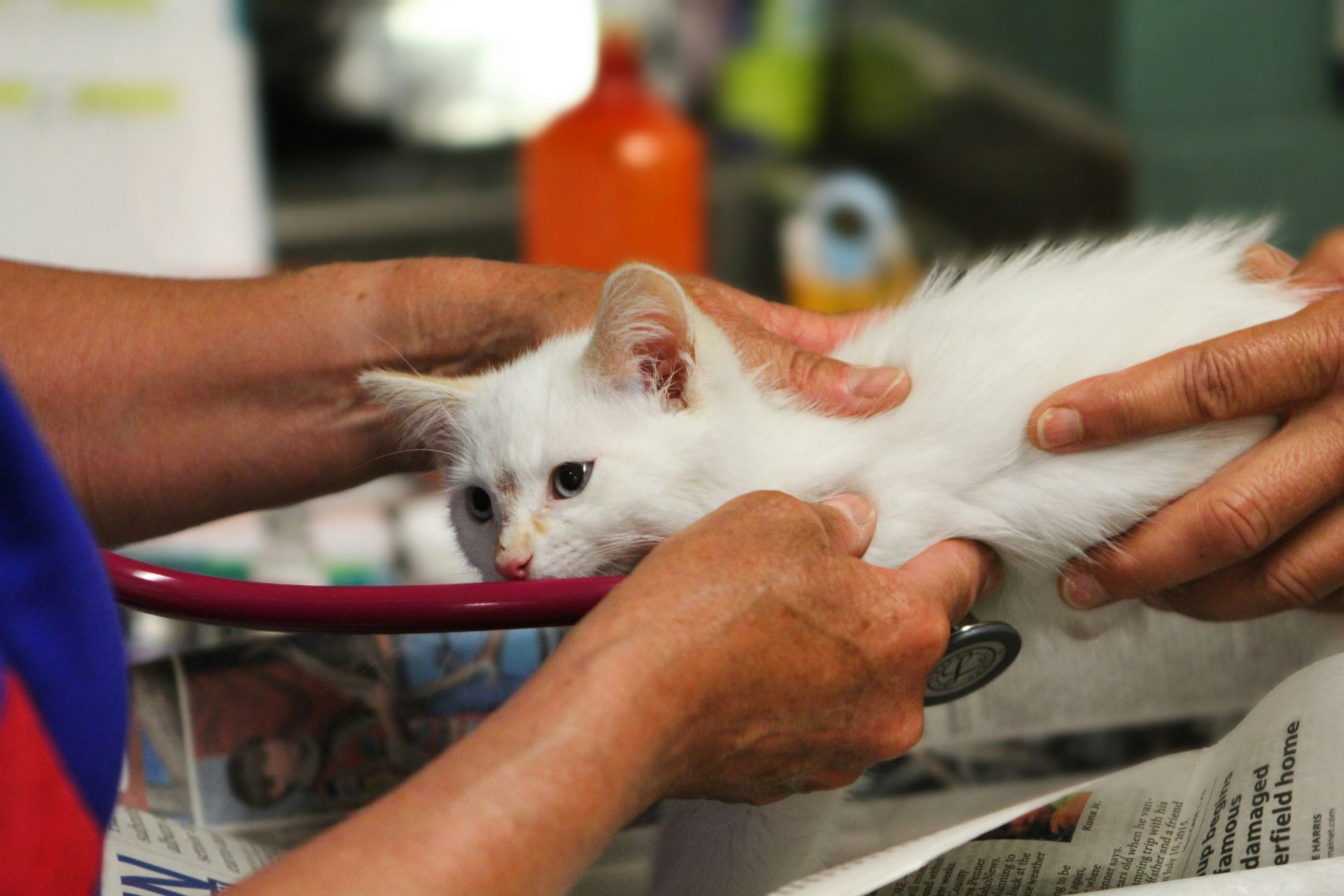
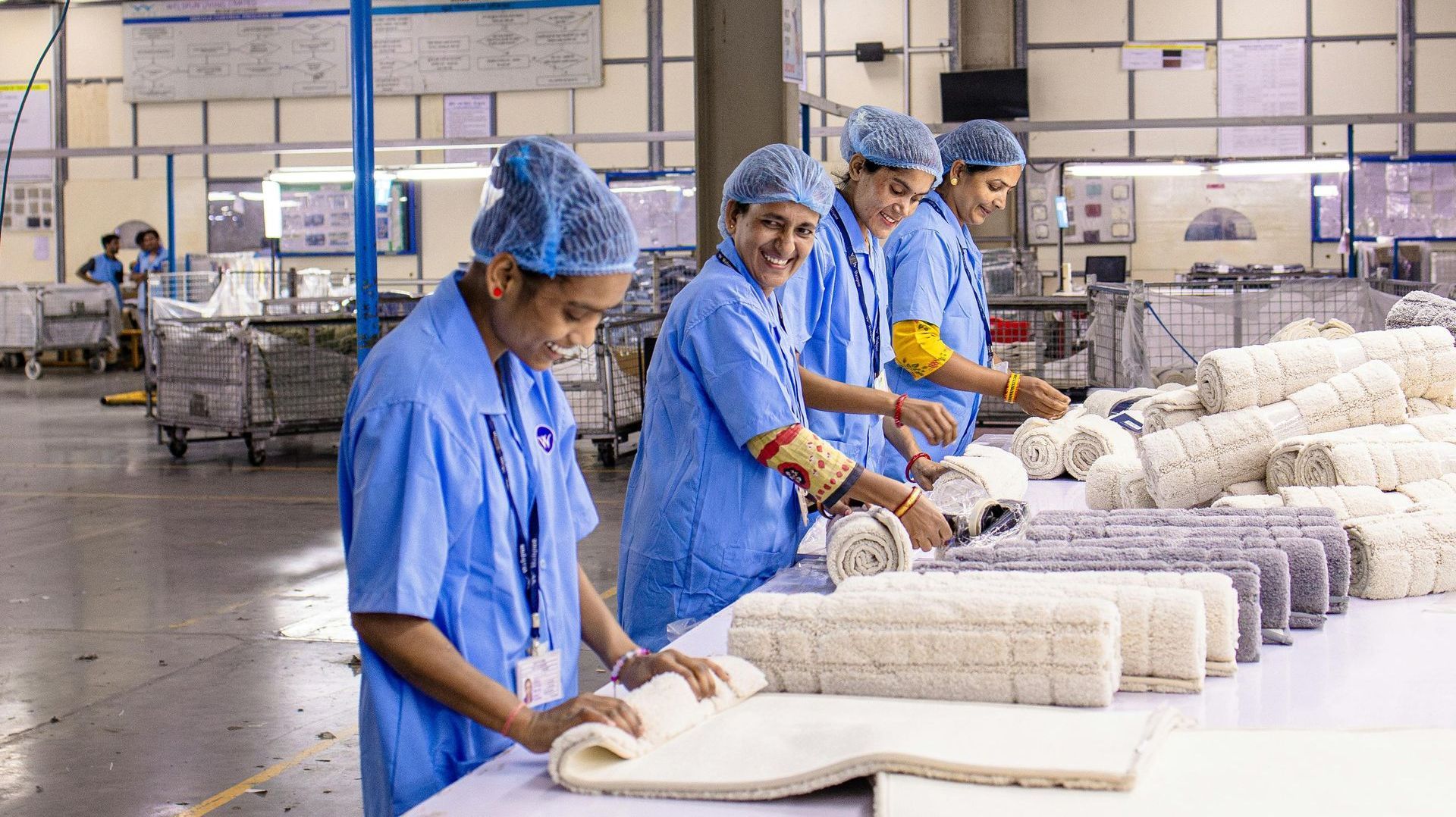
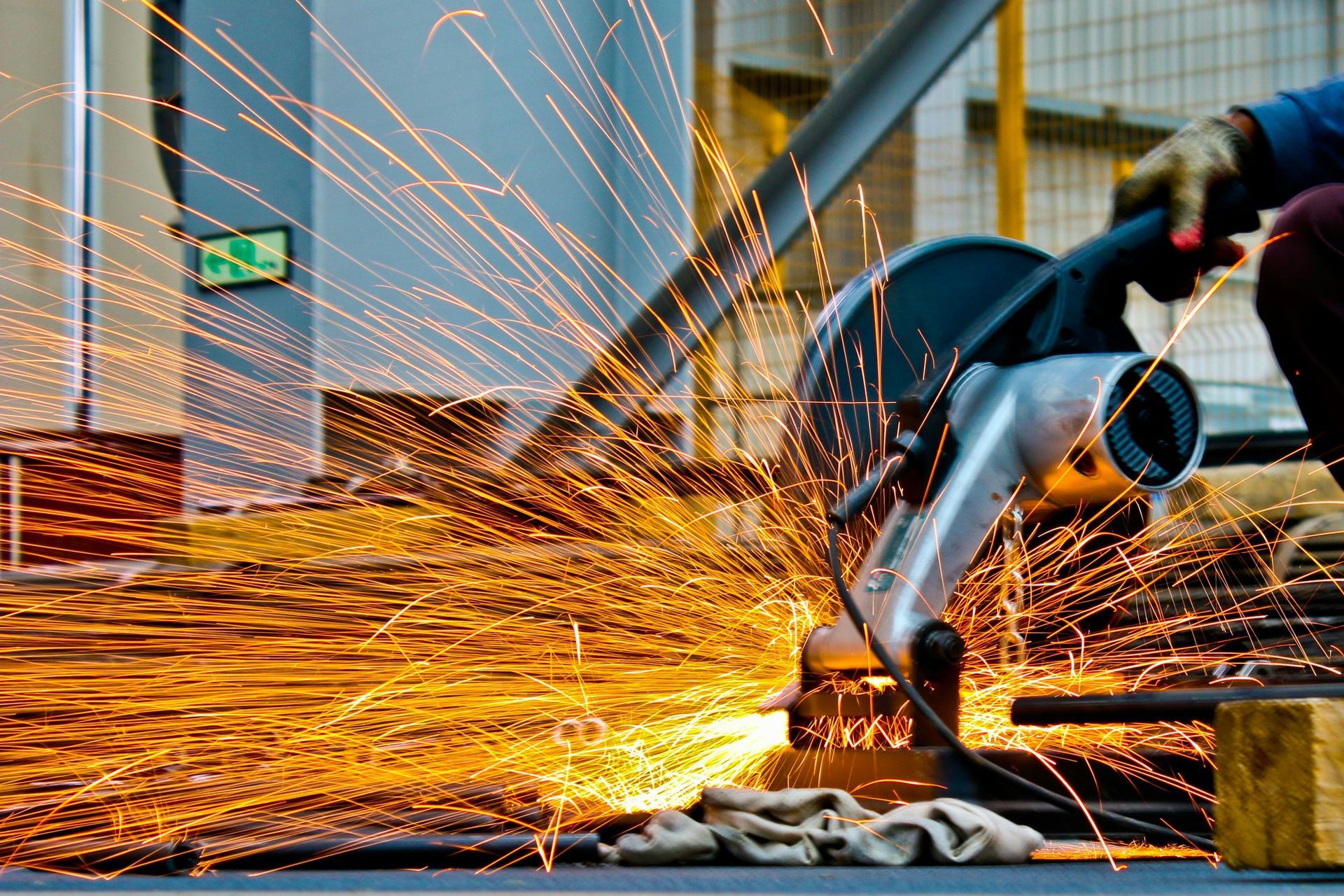
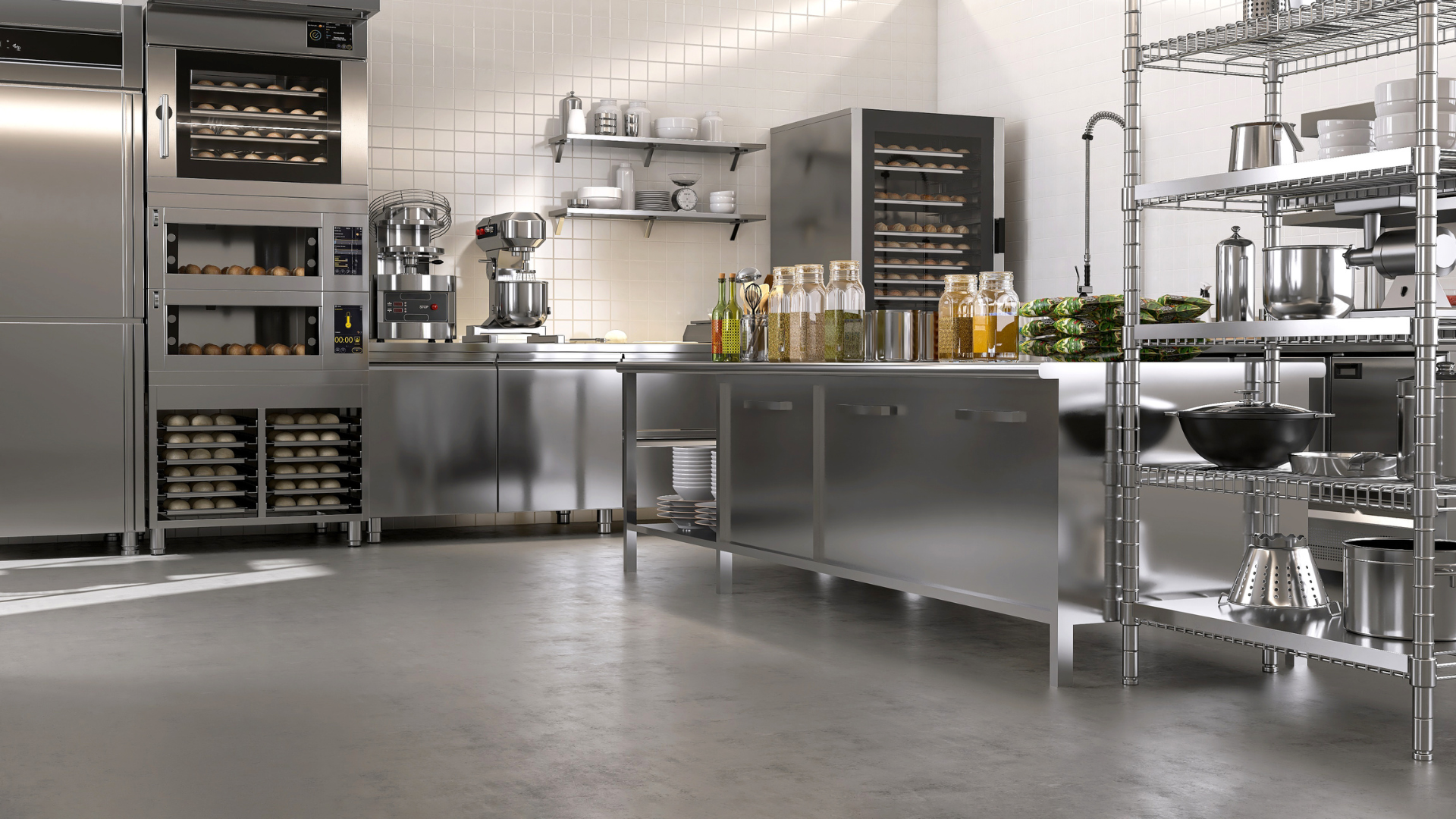
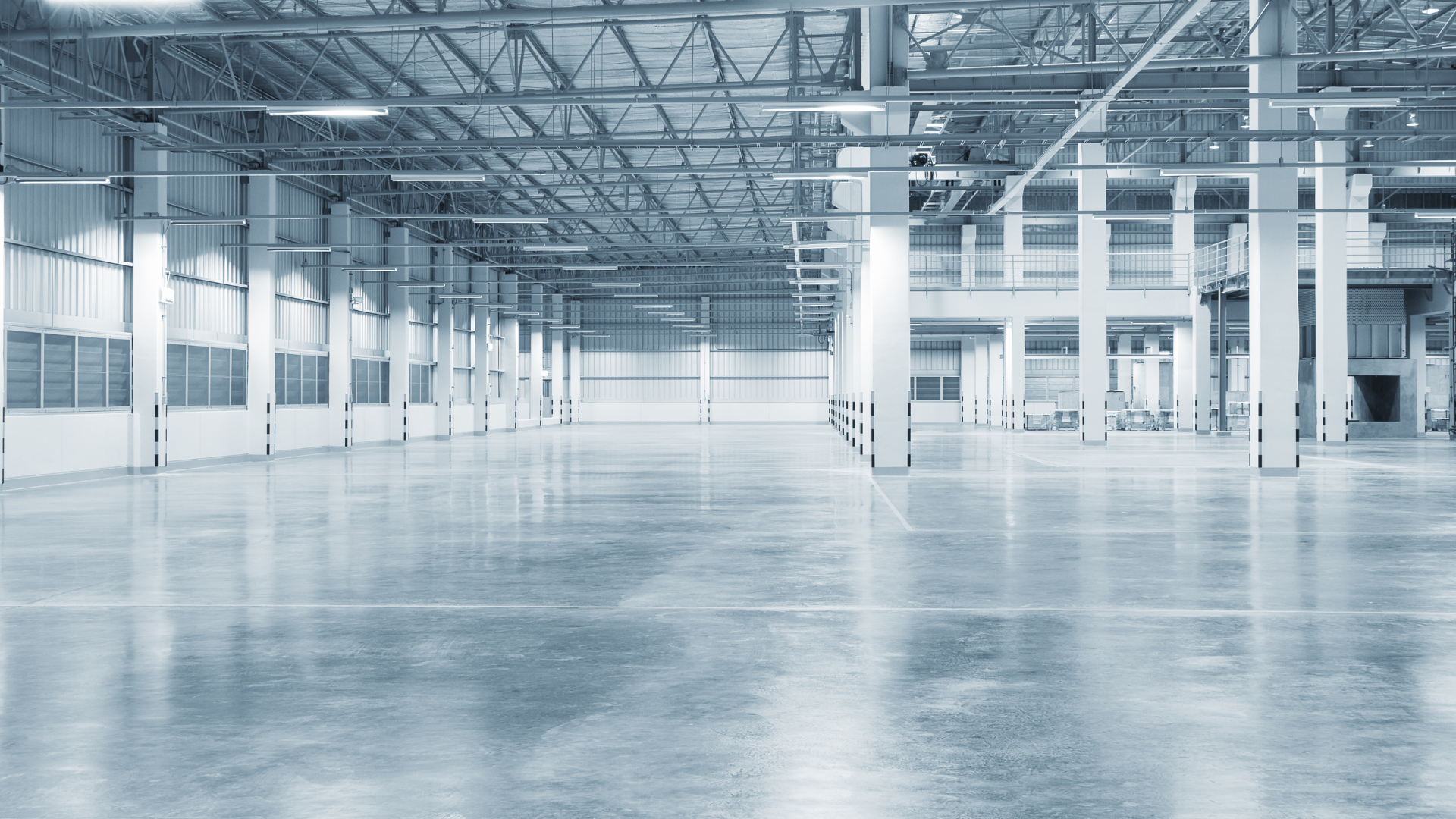
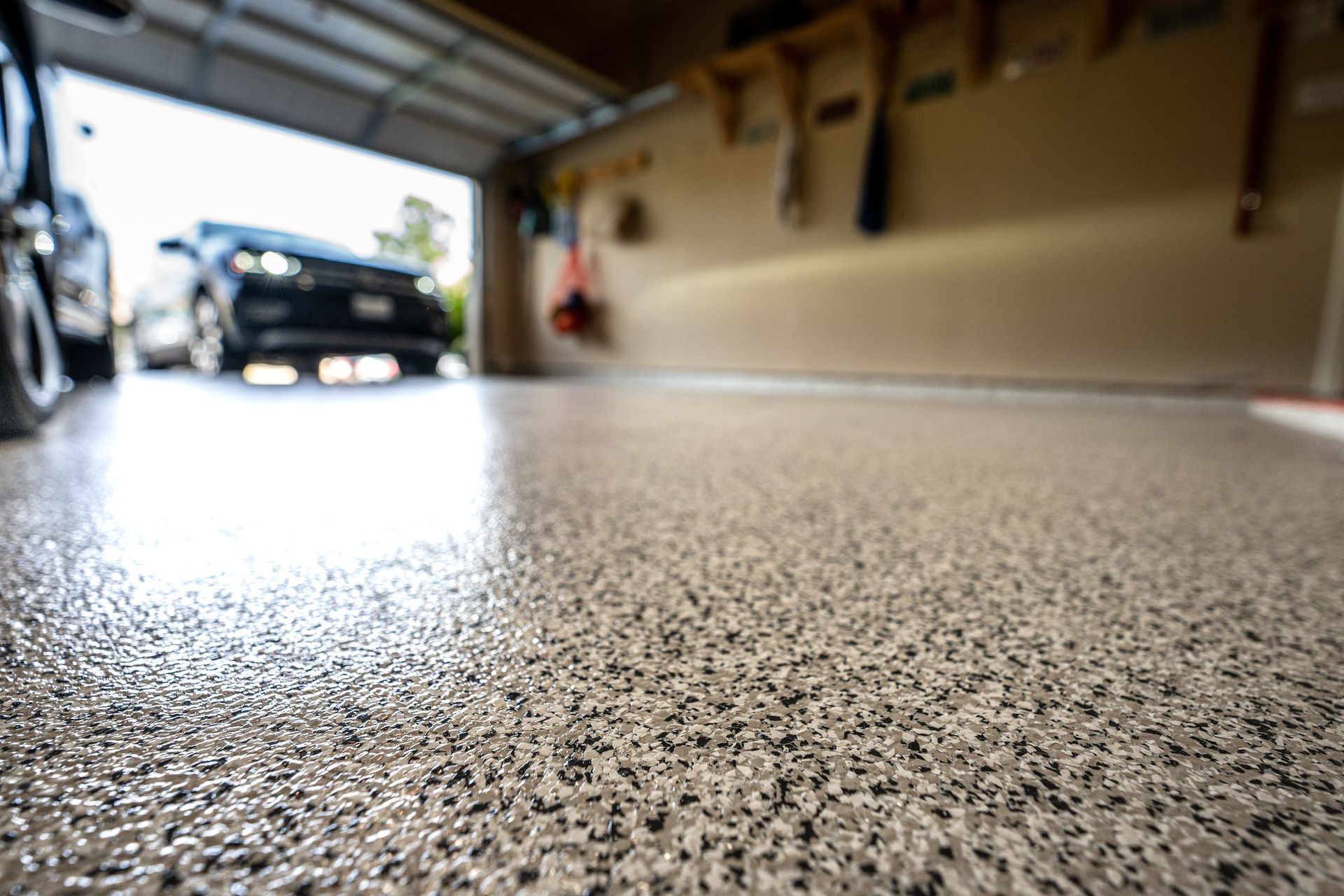
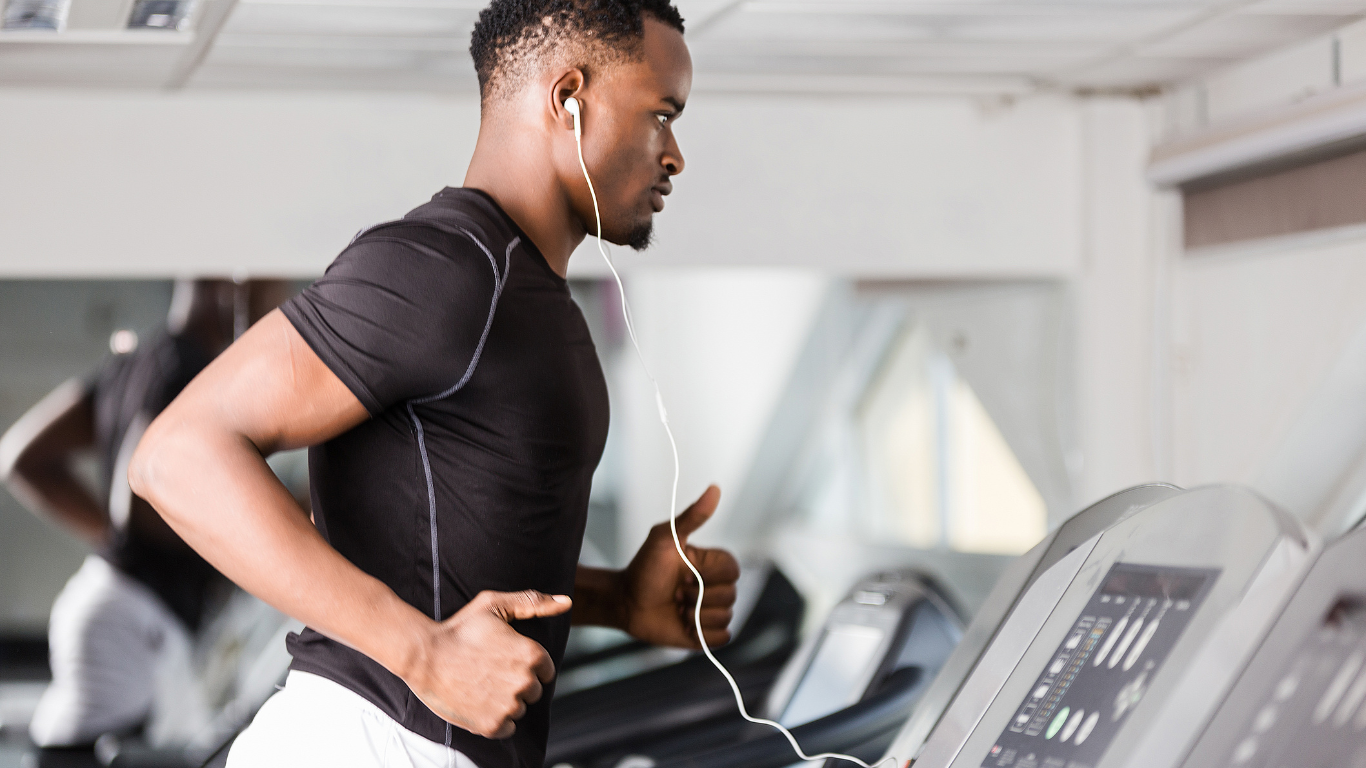
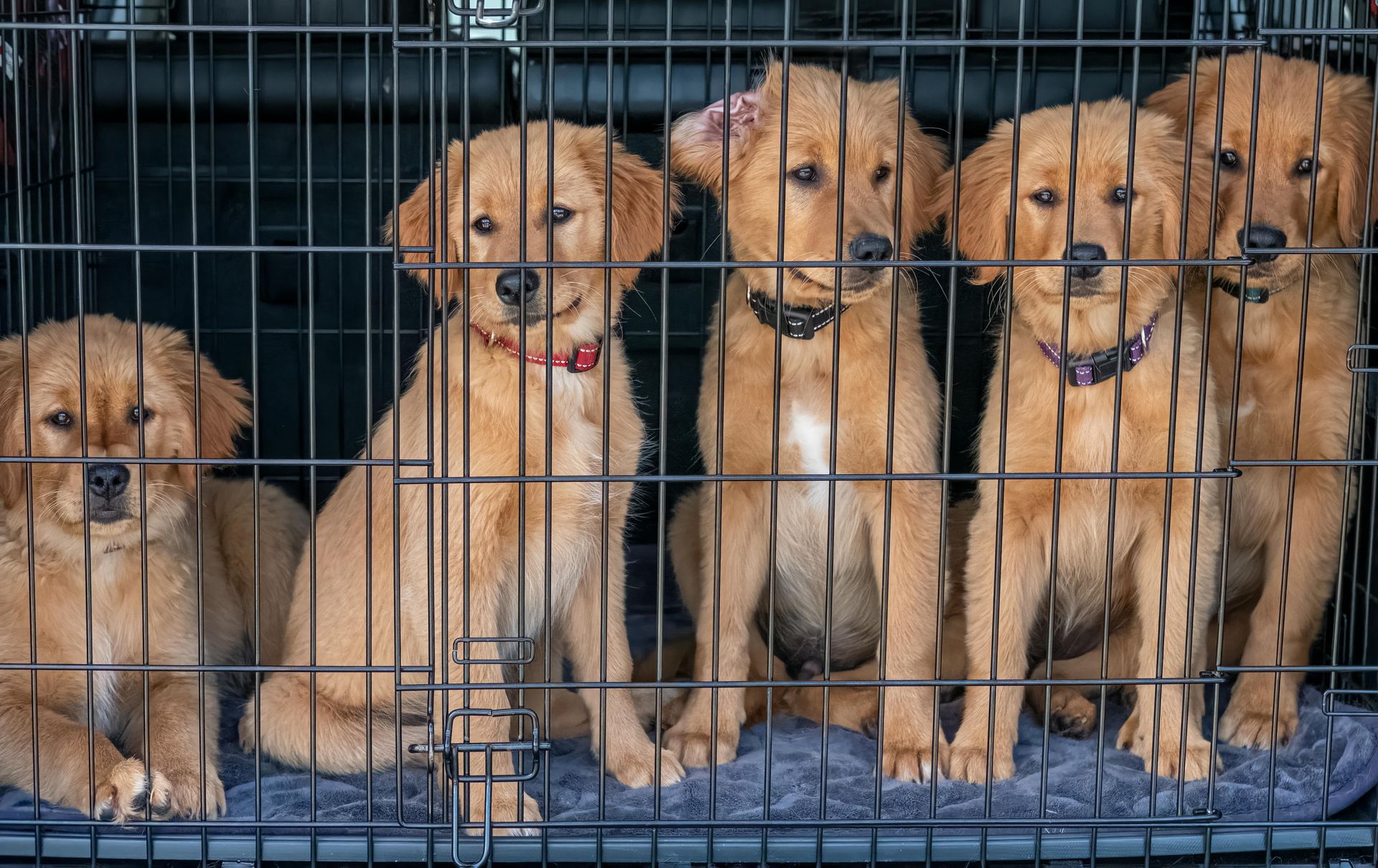
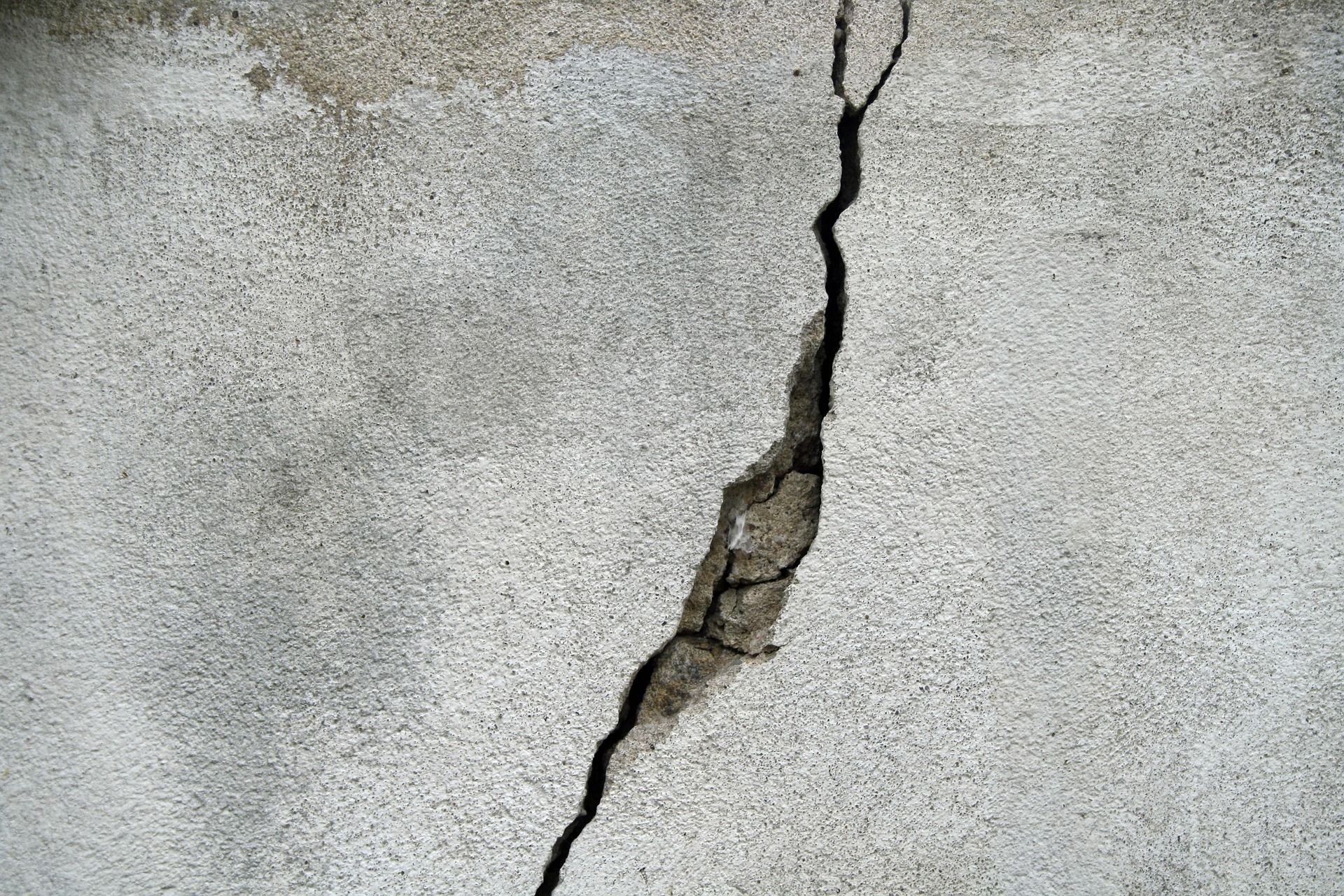